Common Issues Fixed by Packaging Machine Repair Services
Common Issues Fixed by Packaging Machine Repair Services
Blog Article
The Ultimate Overview to Packaging Maker Repair Work: Keep Your Workflow Running Smoothly
Recognizing the complexities of packaging device repair service is crucial for maintaining optimal performance and minimizing interruptions. Normal upkeep not just extends the life of these machines yet additionally addresses typical issues that can hamper performance.
Importance of Routine Upkeep
Regular maintenance of product packaging devices is vital for ensuring optimal performance and durability. By implementing an organized maintenance routine, operators can recognize prospective concerns before they escalate right into considerable issues. This positive method not just decreases downtime yet additionally prolongs the life expectancy of the devices, eventually leading to lowered operational prices.
Regular evaluations allow for the analysis of essential components such as seals, belts, and sensors. Dealing with deterioration without delay avoids unforeseen failings that can interfere with production and result in expensive repair work. In addition, routine upkeep helps ensure conformity with market standards and guidelines, promoting a safe workplace.
Moreover, maintenance activities such as calibration, cleansing, and lubrication considerably improve maker efficiency. Boosted performance translates to consistent product quality, which is crucial for maintaining client complete satisfaction and brand credibility. A properly maintained product packaging device runs at optimal rates and lowers product waste, adding to overall efficiency.
Usual Packaging Device Issues
Product packaging devices, like any intricate machinery, can run into a selection of common issues that might prevent their performance and performance - packaging machine repair. One widespread trouble is inconsistent sealing, which can bring about item spoilage and wastefulness if plans are not effectively sealed. This usually results from misaligned components or used sealing components
One more constant problem is mechanical jams, which can occur because of international things, used parts, or inappropriate positioning. Jams can cause delays in production and rise downtime, ultimately impacting total performance. In addition, digital breakdowns, such as failing in sensors or control systems, can interrupt operations and lead to incorrect dimensions or irregular device behavior.
Additionally, issues with item feed can likewise arise, where items might not be delivered to the packaging location consistently, causing interruptions. Lastly, wear and tear on rollers and belts can lead to suboptimal efficiency, requiring instant focus to prevent additional damages.
Understanding these common concerns is important for maintaining the stability of product packaging operations, guaranteeing that equipment runs efficiently and effectively, which consequently helps in meeting manufacturing targets and preserving product top quality.
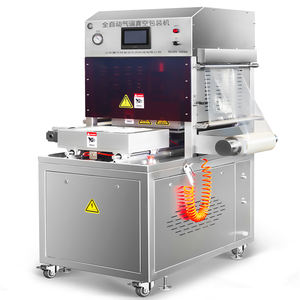
Repairing Methods
Effective repairing techniques are crucial for quickly attending to problems that develop with product packaging devices. A methodical strategy is crucial for identifying the source of malfunctions and decreasing downtime. Begin by gathering information regarding the symptoms observed; this might include uncommon sounds, functional delays, or mistake codes presented on the equipment's interface.
Next, describe the equipment's guidebook for repairing standards specific to the version concerned. This source can provide beneficial understandings right into usual issues and advised analysis steps. Utilize visual assessments to examine for loosened links, used belts, or misaligned components, as these physical factors usually add to operational failings.
Implement a process of elimination by screening individual equipment features. If a seal is not forming properly, evaluate the sealing system and temperature level setups to identify if they satisfy functional specifications. Record each action taken and the results observed, as this can assist in future troubleshooting efforts.
Repair service vs. Replacement Decisions
When encountered with equipment malfunctions, determining whether to replace a product packaging or repair maker can be a facility and critical selection. This choice pivots on numerous vital aspects, including the age of the equipment, the degree of the damages, and the projected effect on functional performance.
First of all, think about the maker's age. Older devices may need even more constant repair services, leading to higher cumulative prices that can go beyond the financial investment in a new device.
Operational downtime is one more crucial factor to consider. Spending in a brand-new equipment that uses boosted performance and integrity might be extra sensible if repairing the equipment will certainly trigger long term delays. Take into consideration the accessibility of components; if substitute components are difficult to come by, it might be a lot more calculated to change the maker entirely.
Eventually, executing a cost-benefit analysis that consists of both long-term and immediate implications will help in making an educated decision that straightens with your financial restraints and functional objectives. (packaging machine repair)
Safety Nets for Durability

Key preventive actions consist of regular lubrication of Full Report moving parts, placement checks, and calibration of controls and sensing units. Establishing a cleansing schedule to get rid of particles and contaminants from machinery can substantially minimize wear and tear (packaging machine repair). In addition, keeping track of operational specifications such as temperature level and resonance can help discover abnormalities early on
Training staff to acknowledge signs of wear or breakdown is one more crucial component of precautionary maintenance. Empowering operators with the understanding to do basic troubleshooting can bring about quicker resolutions and decrease functional disruptions.
Paperwork of maintenance activities, consisting of service records and examination findings, promotes accountability and promotes educated decision-making regarding repair work and substitutes. By focusing on preventative actions, services can guarantee their product packaging machines operate at peak performance, ultimately causing boosted efficiency and minimized functional prices.
Verdict
In conclusion, the effective repair and maintenance of packaging equipments are paramount for maintaining functional effectiveness. Normal upkeep mitigates the risk of usual problems, such as inconsistent securing and mechanical jams, while methodical troubleshooting methods help with timely resolution of breakdowns. Moreover, careful you could check here consideration of repair work versus replacement decisions adds to cost-efficient management of sources. By carrying out safety nets, businesses can boost device long life and guarantee continuous efficiency in packaging operations.
Understanding the details of packaging maker repair work is essential for preserving ideal efficiency and minimizing interruptions.Regular maintenance of product packaging devices is essential for guaranteeing optimal efficiency and long life.Product packaging equipments, like any kind of complicated equipment, can encounter a range of typical issues that may hinder their performance and efficiency. If fixing the maker will trigger prolonged hold-ups, investing in a brand-new machine that provides improved effectiveness and dependability may be more sensible.In verdict, the efficient maintenance and repair work of product packaging devices are critical for maintaining operational performance.
Report this page